基于虚拟仪器的离合器膜片弹簧参数测试系统的实验研究
时间:2018-06-14 17:40:07
手机看文章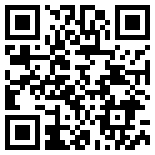
扫描二维码
随时随地手机看文章
[导读]
1系统硬件设计
该测试系统的整体结构为门式结构,在工作台上加装液压系统实现自动控制(图1),测试系 统硬件主要有工作台、横梁和立柱组成其加载框架。加载框架支承在箱体总成上。加载缸固 定在工作
1系统硬件设计
该测试系统的整体结构为门式结构,在工作台上加装液压系统实现自动控制(图1),测试系 统硬件主要有工作台、横梁和立柱组成其加载框架。加载框架支承在箱体总成上。加载缸固 定在工作台下的箱体中,其活塞杆穿过工作台。下压头固定在加载缸的活塞杆上,其动作范 围由行程开关调节。上油缸固定在调整螺杆上,调整螺杆由两个螺母固定在横梁上。上压头 通过油缸和力传感器与调整螺杆联结。调整螺杆可以根据不同型号弹簧所需要的空间上下调 整。固定在油缸下部的位移传感器A用于测量弹簧轴向受力时的整体变形。工作台上的三个 位移传感器B1~B3用于测量弹簧大端的变形量。力传感器用来测量加在膜片弹簧上的载 荷。这5路传感器信号经过信号调理电路后传送给数据采集卡,Labview(虚拟仪器软件)对其 处理后得到膜片弹簧的两个重要的特性曲线—负荷特性曲线和分离特性曲线;并根据实际需 要,在系统的操作界面上给出离合器盖总成参数的特征点,以便工程技术人员判断离合器的 工作性能。?
(1)负荷特性测量原理是将弹簧放在工作台上,工作台支承在弹簧的大端面上。这 时,上油缸活塞处于上止点,加载缸上行。上压头压在弹簧上支承环上,加载缸继续上行, 这时测量弹簧大端位移λ1(位移传感器A)及压力P1(力传感 器),即可得到负荷特性曲线(P1-λ1曲线)。?
虚拟仪器软件有前面板和框图程序两部分。前面板主要完成可视化人机交互功能,来模拟真 实仪器的前面板。每一个程序的前面板都有相应的框图程序与之对应,它采用图形化的编程 语言编写,可以理解成传统程序的源代码。主要完成数据的采集、分析和处理过程。
软件在设计过程中采用了高速磁盘流技术,便于事后对数据进行回放和分析。另外,如果在 数据采集的过程中对数据进行各种分析会占用CPU大量时间,导致数据采集出现误差。必须 对数据进行高速保存。图2所示的框图程序为本系统的数据采集模块。首先利用Oper/Create /ReplaceFile.vi模块创建一个数据流文件,然后利用AI Config.vi模块对DAQ设备进行配置 ,用AI Start Config.vi模块启动DAQ,利用一个While循环和AI Read Config.vi模块将数 据不停的从DAQ的缓存中读出,然后AI Write Config.vi模块将数据写入到磁盘中。在数据 采集完成后,利用AI Config.vi模块读出数据进行分析和处理,最后用AIClear.vi来结束整 个系统的执行,释放资源。
软件在设计过程中采用了高速磁盘流技术,便于事后对数据进行回放和分析。另外,如果在 数据采集的过程中对数据进行各种分析会占用CPU大量时间,导致数据采集出现误差。必须 对数据进行高速保存。图2所示的框图程序为本系统的数据采集模块。首先利用Oper/Create /ReplaceFile.vi模块创建一个数据流文件,然后利用AI Config.vi模块对DAQ设备进行配置 ,用AI Start Config.vi模块启动DAQ,利用一个While循环和AI Read Config.vi模块将数 据不停的从DAQ的缓存中读出,然后AI Write Config.vi模块将数据写入到磁盘中。在数据 采集完成后,利用AI Config.vi模块读出数据进行分析和处理,最后用AIClear.vi来结束整 个系统的执行,释放资源。
应用本系统对某厂家的膜片弹簧进行了多次实验,通过其测试结果可以直观的分析膜片弹簧 的负荷特性、分离特性以及具体的参数,图3是两片不同规格的膜片弹簧的分离特性的对比 关系(应用本系统的多曲线对比分析模块分析的结果)。其测试结果与离合器出厂时的标定参 数基本一致。虚拟仪器技术的应用减少了传统仪器在信号传递过程中带来的误差,有很高的 精确性和稳定性;此外,基于框图程序编程的技术还具有组态灵活、功能扩展性强、信息交 换方便、维护费用低和开发周期短等众多优点,因而,势必会在各种测试系统中得到广泛的 应用
本站声明: 本文章由作者或相关机构授权发布,目的在于传递更多信息,并不代表本站赞同其观点,本站亦不保证或承诺内容真实性等。需要转载请联系该专栏作者,如若文章内容侵犯您的权益,请及时联系本站删除。
换一批
延伸阅读